Understanding OEM Metal Cutters: A Comprehensive Guide
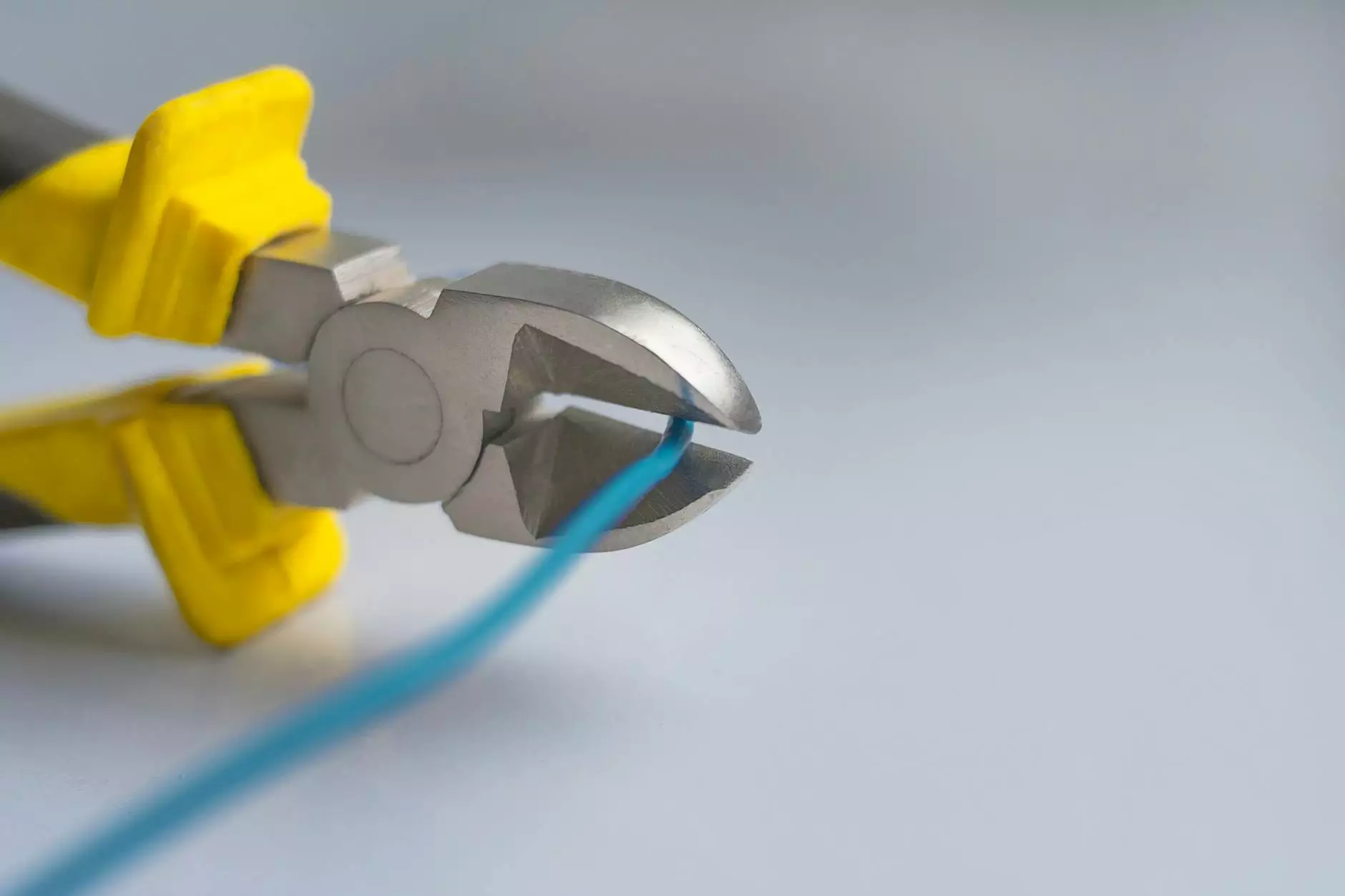
What is an OEM Metal Cutter?
An OEM metal cutter is a specialized tool designed for cutting metal materials accurately and efficiently. OEM stands for Original Equipment Manufacturer, indicating that these cutters are often designed and produced per specific requirements meant for particular machinery or production lines. Their purpose serves industries reliant on precision metal fabrication, such as manufacturing, automotive, and aerospace sectors.
The Evolution of Metal Cutting Technology
Over the years, metal cutting technology has evolved significantly. From traditional manual tools to sophisticated CNC machines, the industry has seen continuous advancements. OEM metal cutters integrate modern technologies that allow for high-speed and precision cutting, contributing to improved productivity and cost-effectiveness.
Types of OEM Metal Cutters
Understanding the different types of OEM metal cutters can help manufacturers choose the right tool for their specific needs. Here are some common types:
- Band Saws: Ideal for cutting a variety of metals with precision.
- Plasma Cutters: Utilizes plasma to cut thick metals with speed.
- Water Jet Cutters: Uses high-pressure water jets mixed with abrasives, providing precision without thermal distortion.
- Laser Cutters: Employs focused laser beams for exact cuts, perfect for intricate designs.
- Shears: A mechanical cutting tool used for straight cuts in thin metal sheets.
Applications of OEM Metal Cutters
OEM metal cutters play a crucial role across various industries. Here are some of their prominent applications:
1. Automotive Industry
In the automotive sector, metal cutters are used to produce components such as chassis, engine parts, and body panels, ensuring that parts are manufactured with accuracy to meet strict industry standards.
2. Aerospace Manufacturing
The aerospace industry requires incredibly precise and lightweight components. OEM metal cutters are used to shape and form critical parts like wings and fuselages, where accuracy can affect overall performance and safety.
3. Construction and Fabrication
From structural steel to metal framing, OEM metal cutters are invaluable in construction and fabrication. They enable builders to create strong, reliable frameworks and other essential components.
4. Electronics Manufacturing
The electronics industry utilizes metal cutters for enclosures, connectors, and circuit board components that require accuracy and reliability.
Benefits of Using OEM Metal Cutters
Investing in OEM metal cutters presents numerous advantages for manufacturing businesses:
- Precision and Accuracy: Custom-designed OEM cutters ensure exact specifications.
- Increased Efficiency: Faster cutting processes lead to higher output with less downtime.
- Cost-Effectiveness: Reducing material waste and improving yield save money in the long run.
- Durability and Longevity: OEM cutters are often built with high-quality materials that withstand substantial use.
Choosing the Right OEM Metal Cutter
When it comes to selecting the most suitable OEM metal cutter for your needs, consider the following factors:
Material Type
Different materials require different cutting methods. Ensure that your cutter is compatible with the types of metals you will be working with.
Thickness of Metal
The thickness of the metal will influence the type of cutter you require to achieve optimal results.
Cutting Precision and Tolerances
Evaluate how precise your cuts need to be. For applications requiring high precision, laser or water jet cutters might be more appropriate.
Production Volume
High production volumes may necessitate faster, automated cutters, while low-volume needs could be met with more manual options.
Maintenance of OEM Metal Cutters
Proper maintenance of your OEM metal cutter ensures efficiency and prolongs its lifespan:
Regular Cleaning
Keep your equipment free from debris and metal shavings to maintain operational efficiency.
Sharpening and Blade Replacement
Regularly check blades and cutters for wear. Sharpening or replacing these components is crucial for maintaining cutting precision.
Lubrication
Apply lubricant according to the manufacturer's guidelines to ensure smooth operation and reduce wear.
Future Trends in OEM Metal Cutting
The landscape of metal cutting technology is ever-evolving. Here are some anticipated trends that may shape the future of OEM metal cutters:
- Increased Automation: As technology develops, more processes will be automated, promoting consistent quality and speed.
- Integration of Artificial Intelligence: AI could play a role in optimizing cutting paths and improving efficiency in real-time.
- Eco-friendly Innovations: Sustainable manufacturing practices will lead to more energy-efficient and environmentally friendly cutting technologies.
Conclusion
In conclusion, OEM metal cutters are indispensable in the metal fabrication industry. With their ability to enhance precision, increase efficiency, and reduce overall costs, they represent an essential tool for manufacturers globally. Companies like SZBlade provide high-quality OEM metal cutters tailored to meet the unique demands of various industries. Embracing these technologies will not only help businesses innovate their production processes but also secure a competitive edge in the market.