CNC Lathe Factory: Precision Engineering in Metal Fabrication
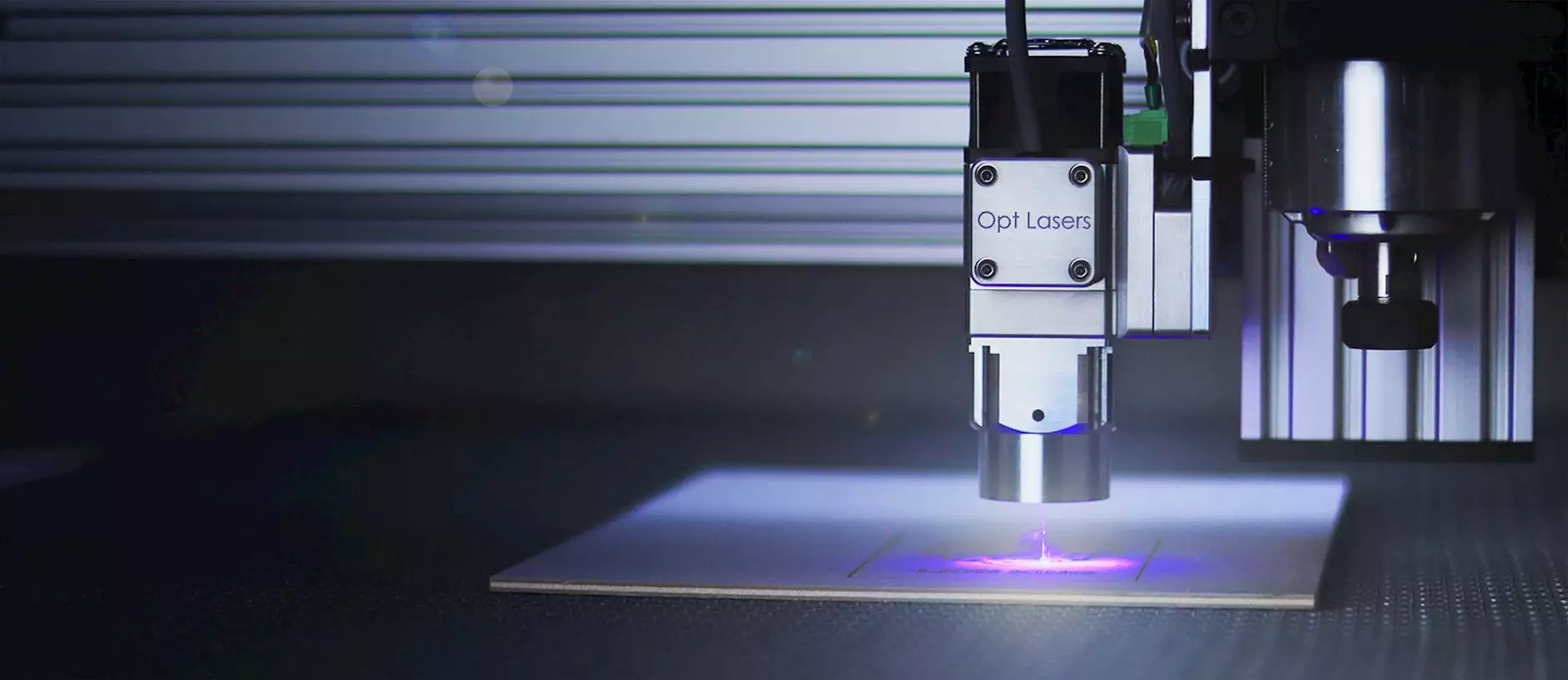
The world of metal fabrication is continually evolving, with CNC lathe factories at the forefront of innovation and precision. As businesses strive for efficiency and accuracy, the importance of CNC (Computer Numerical Control) technology has become increasingly apparent. In this comprehensive article, we will delve deep into the workings of a CNC lathe factory, the advantages it offers, and why investing in such technology is essential for modern manufacturing.
Understanding CNC Lathe Technology
A CNC lathe is a sophisticated machine tool that utilizes computer-controlled systems to achieve highly accurate cuts and shapes in metal products. Unlike traditional lathes, which require manual operation, CNC lathes operate on programmed instructions, enabling consistent and repeatable results. This technology is instrumental in various industries, particularly in metal fabrication, where precision is paramount.
The Mechanism of a CNC Lathe
The CNC lathe operates using a combination of mechanical and electronic parts. Here's a brief overview of its primary components:
- Controller: The brain of the CNC lathe, which interprets the G-code instructions to guide the lathe's operations.
- Spindle: This component rotates the workpiece at high speeds, allowing for efficient material removal.
- Tool Holder: Holds the cutting tool in place, allowing it to move precisely across the workpiece.
- Bed: The base of the lathe, which provides stability and supports other components.
The Advantages of CNC Lathe Factories
Investing in a CNC lathe factory offers numerous benefits that can enhance production efficiency and product quality. Here are some key advantages:
1. Precision and Accuracy
CNC lathes provide unparalleled precision compared to manual lathes. With the ability to execute complex designs and exact specifications, these machines reduce the margin of error significantly, resulting in higher quality products.
2. Increased Production Speed
Automation in CNC lathe factories enables faster production cycles. Components can be fabricated rapidly without compromising on quality, making it an ideal solution for high-volume manufacturing.
3. Cost Efficiency
By reducing labor costs and minimizing waste, CNC lathe factories can significantly enhance the cost-effectiveness of production processes. Automated workflows allow for better resource management and lower operating costs over time.
4. Versatility
CNC lathes can work with various materials, including metals, plastics, and composites, making them suitable for a wide range of applications. From automotive parts to medical devices, CNC lathes can handle diverse projects with ease.
5. Enhanced Safety
With automation and controlled processes, CNC lathe factories reduce the risks associated with manual machining operations. Enhanced safety features protect operators from accidents and injuries.
Key Applications of CNC Lathe Technology in Metal Fabrication
CNC lathe technology plays a critical role in various sectors. Below are some prominent applications:
1. Automotive Industry
The automotive sector relies heavily on CNC lathe factories for manufacturing precision components such as axle shafts, gears, and engine blocks. These components require utmost precision to ensure safety and performance.
2. Aerospace Engineering
In aerospace, the demands for light-weight yet durable components are met through advanced CNC machining. Parts like turbine blades and structural components benefit from the precision and reliability offered by CNC lathes.
3. Medical Devices
Highly specialized medical devices, including surgical instruments and prosthetics, require meticulous craftsmanship. CNC lathe factories ensure that these critical components meet stringent quality standards.
4. Electronics
The electronics industry utilizes CNC lathes for fabricating housings, casings, and other intricate components that must fit precisely to ensure functionality and reliability.
The Future of CNC Lathe Factories
The future of CNC lathe factories looks promising, driven by advancements in technology and the growing demand for precision engineering. Here are some trends shaping the industry:
1. Integration of AI and Machine Learning
Manufacturers are increasingly leveraging AI and machine learning to enhance CNC operations. These technologies can predict machine failures, optimize manufacturing processes, and streamline production schedules.
2. 3D Printing and Hybrid Technologies
As manufacturers explore the benefits of 3D printing, the integration of CNC lathes and additive manufacturing equipment is on the rise. This hybrid approach allows for the creation of complex geometries that traditional methods cannot achieve.
3. Sustainable Practices
With environmental concerns at the forefront, CNC lathe factories are adopting sustainable practices, such as reducing waste and implementing energy-efficient solutions. Utilizing renewable materials and recycling waste are becoming industry standards.
Conclusion: Embracing CNC Lathe Technology for Success
In conclusion, the role of CNC lathe factories in the metal fabrication industry is indispensable. With their ability to deliver unmatched precision, efficiency, and versatility, these facilities are essential for businesses aiming to stay competitive in an increasingly demanding market.
Investing in a CNC lathe factory not only enhances productivity but also opens doors to new opportunities across various sectors, from automotive to aerospace and beyond. As DeepMould.net continues to lead the way in metal fabrication, embracing advanced CNC technology is a critical step toward future success.